
Product Description: | szl coal fired boiler |
Rated evaporation (t/h): | coal-fired boilers |
Project boiler medium: | steam boiler |
Equipment: | SZL30-1.25-AII |
Boiler water wall tubes coal fired boiler
Mechanism of high temperature corrosion and leakage of boiler membrane wall tube
The high sulfur content in fuel coal is the main factor for sulfur corrosion. Mm. The medium in the tube is superhot water, the temperature is no more than 350℃, the pressure is 11.28MPa, the medium outside the tube is high-temperature flue gas in the furnace, the flame temperature is 950℃, and the flue gas contains certain amount of CO, CO2, SO2, SO3 and unburned coal powder. Sulfur corrosion in membrane fireplace tubes is premised on the presence of more than 1% sulfur in flue gas. Sulfide corrosion, sulfate corrosion and sulfuric acid coke corrosion.
Therefore, the corrosion rate increases with the increase of temperature in the reduction atmosphere caused by the high-temperature corrosion of water-cooled wall tube. Pulverized coal begins to break off near the molten state of the membrane hearth tube, and the boundary layer accumulates carbon and sulfur. The difficult situation of the formation of combustible sulfur trioxide and sulfur occurred due to the formation of reductive atmosphere due to local hypoxia, and the free sulfur and sulfide (hydrogen sulfide, etc.) began to react with iron, causing corrosion of the pipe wall. Corrosion thinned the outer wall of the water-cooled wall tube and filled the wedge crack with corrosion products such as iron sulfide and iron oxide.
Concept of Boiler water wall tubes coal fired boiler
Under the action of axial alternating stress, the water-cooled wall tube will undergo creep/stress rupture and produce transverse crack
Boiler water wall tube will suffer from low cycle (thermal stress caused by start-stop), medium cycle (thermal stress caused by the repeated appearance and disappearance of steam film) and high cycle (caused by vibration) alternating stress during operation, resulting in fatigue damage; The thermal shock occurs when the temperature of furnace tube wall changes significantly when water blowing is used. In corrosive environments, flue gas such as sulfur, alkali, alum and chlorine will promote damage; When the thermal load is high, the fatigue and strength of the material will be reduced. Due to the change in the position of the high-temperature flame and the radiant heat of the gas, the metal temperature will be changed. The expansion or contraction in the metal will lead to the alternating stress, and the damage caused by plastic deformation and fatigue crack will accumulate the alternating stress.
At high temperatures, metal strength is relatively low, the amplitude of the stress may exceed the yield boundary of the material, local plastic deformation, and increase with each cycle, so that even a small cycle still has thermal fatigue cracks, and creep fracture stress/corrosion begins.
For detailed boiler quotes, you can consult online customer service or call the 13861509127 hotline.
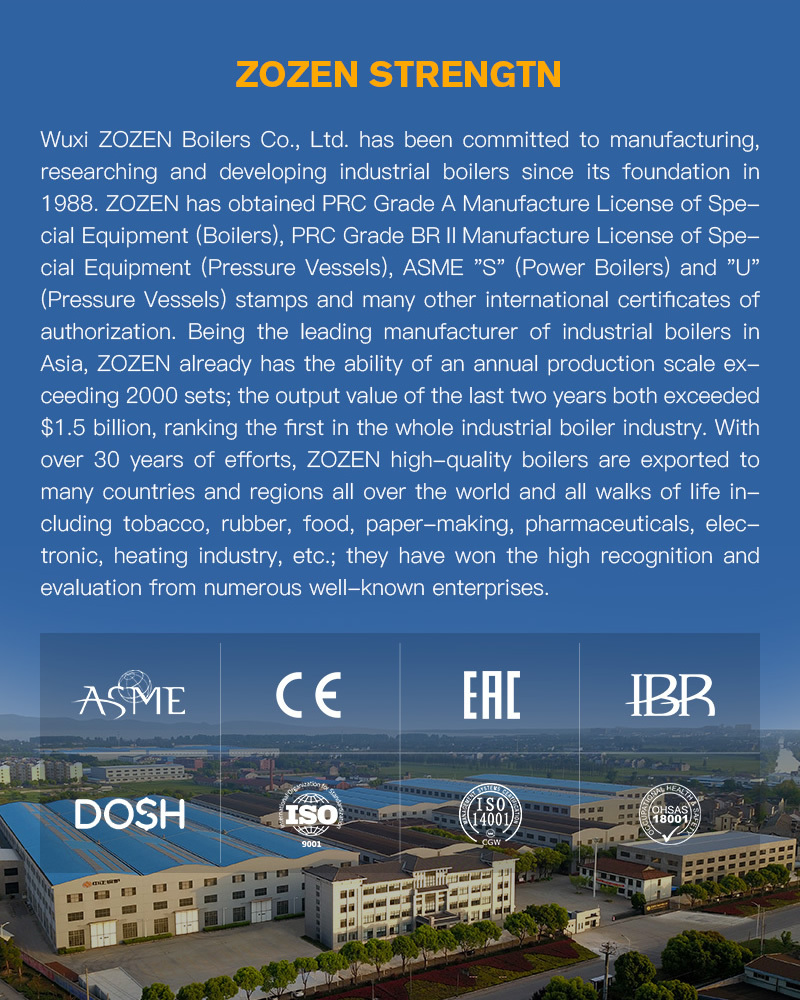
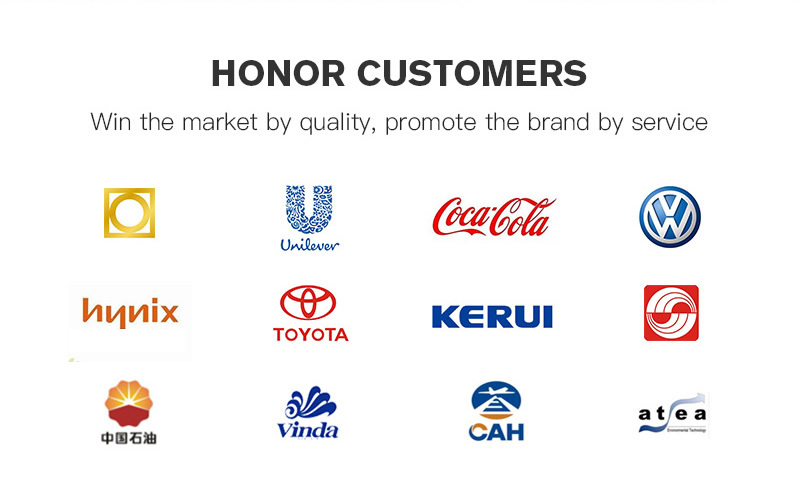